New design and features: IPTE FlexPresser II – solutions for connection technology
With the FlexPresser, IPTE, one of the world's leading suppliers of automation solu- tions for the electronics and mechanics industry, offers innovative, powerful and flexi- ble press-fit solutions for almost every customer application.
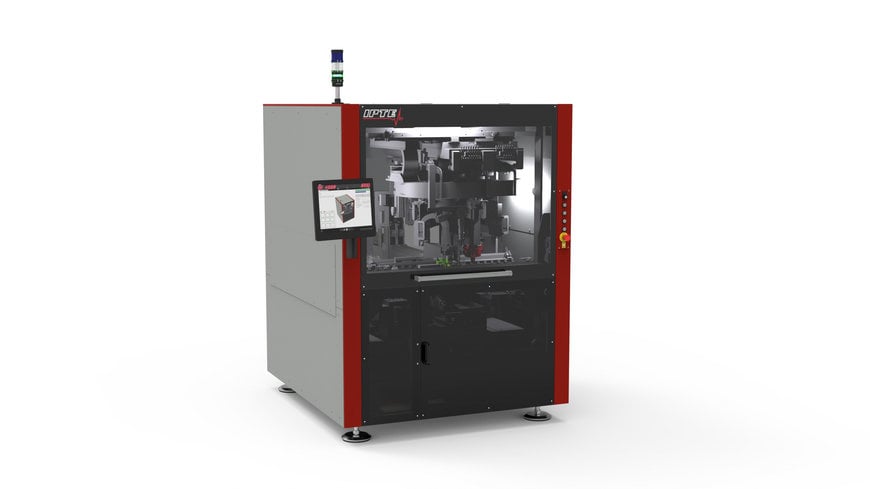
The next generation of this proven machine for the assembly of press-fit contacts, the IPTE FlexPresser II, is based on the High Dynamic Cell, IPTE’s new production cell, and is now available.
The basis of the machine is a cell with a rear feeder bank, for all sorts of component feeding. The most important highlights of the IPTE FlexPresser II are a three-part belt segment for the PCB transport, the highly dynamic linear motors for moving the set- ting unit and a PCB support to absorb the joining forces. High press-in forces of up to 7,000 Newton are possible, due to the adapted cell design.
The IPTE FlexPresser II stands out:
- Designed as a fully automatic inline system and easy to integrate into production lines: Feeding and removal of printed circuit boards with SMEMA inter face.
- Free programmable component positions (x, y, angle of rotation) creates huge flexibility during pickup and press-in, thus not only for layout or component changes purposes.
- The wide feeder bank (max. 12 places) allows the docking of different component feeders such as stick feeders, tray feeders and sorting conveyors. Further customer-specific feeders are easy to integrate.
- Excellent process monitoring through force and travel-dependent pressing-in.
- Easy to adapt to application-specific requirements.
- Press-in forces of up to 7,000 N.
- Low maintenance linear motors allow high dynamic and precise positioning of the setting unit.
- An optional vision scan of the component pins with subsequent position correction compensates component tolerances and improves the quality of the press-in process.
- An automatic gripper quick-change system allows different component types to be pressed in per PCB without operator intervention.
- A quick-change system for the PCB support plate minimizes set-up times for other PCB types.
- Stepless variable press-in speeds allow flexible adaptation to different setting tasks.
- For smooth maintenance access, the component feeders are quickly undocked from the machine and easily re-docked afterwards.
- For process monitoring, the placement process is carried out with a controlled placement force.
High Dynamic Cell – IPTE’s new production cell
IPTE is successively converting all its production cells to the new design. In addition to align to the requirements of Industry 4.0, to introduce a new visual appearance and to optimize the arrangement of machine components, the new generation of IPTE production cells adds another step into the further standardization of the so called standard machines.
The new High Dynamic Cell series is available with a height of two meters, three widths (1 m, 1.5 m & 2 m) and three depths (1.5 m, 1.7 m & 2 m). They are scalable depending on the application and customer requirements. With the new production cells, IPTE offers a powerful and modern concept for the automation of various manufacturing processes in electronics and mechanical pro- duction. This new line contains many improvements compared to the previous gen- eration.
www.ipte.com