electronics-journal.com
16
'20
Written on Modified on
Component carriers simplify the mounting of sensors
HARTING has developed a component carrier that can be mounted directly with electronic components allowing previous manual assembly processes to be automated. Flexible circuit boards can also be replaced, increasing precision and reducing assembly costs.
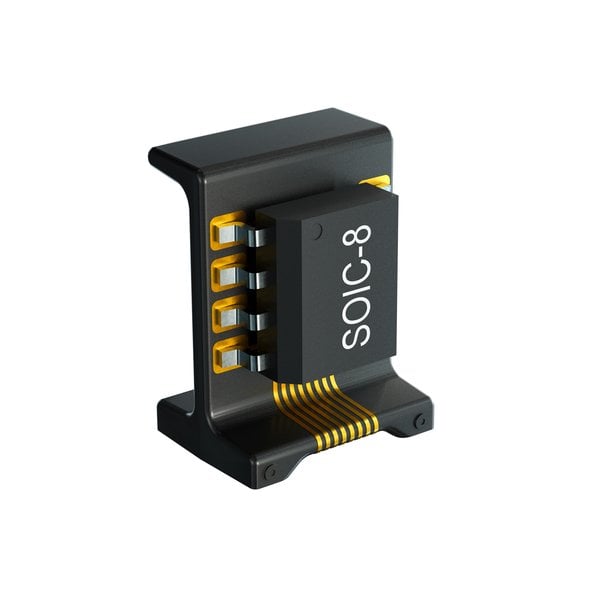
The component carrier serves as a connecting element between a printed circuit board (PCB) and electronic components (such as LEDs, ICs, photo–diodes or sensors).
Automatic mounting of position sensors
In electrical drives, Hall sensors are used to determine the exact position of the rotor and the electronic components are normally attached manually as wired THT components. A mechanical bracket is also mounted which aligns the sensors at an angle of precisely 90 degrees.
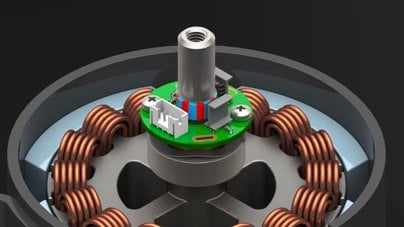
Two-channel Hall-effect encoder for recording the rotation of a motor shaft
Such manual assemblies are no longer necessary when HARTING's component carriers are used because the sensors are automatically mounted onto the component carrier, making an additional component for arranging and aligning the sensors unnecessary.
The component carrier with the position sensors is delivered by HARTING in a blister belt packaging (tape & reel) for the automatic SMD assembly process. This component carrier replaces the manual processing steps – thus increasing the reproducibility and reducing the processing costs.
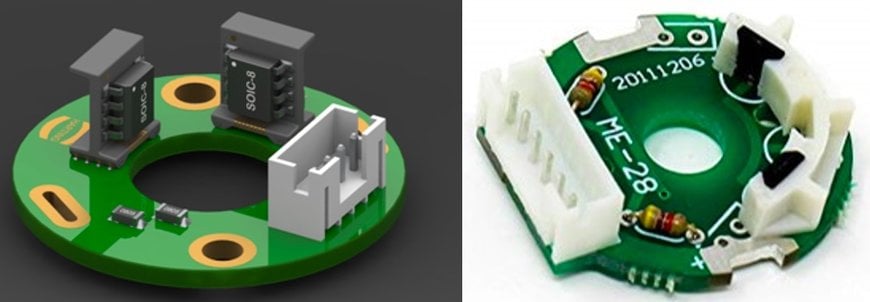
Component carrier solution & traditional solution