electronics-journal.com
11
'21
Written on Modified on
Driving the Mars Rover
Behind the scenes of space-worthy motor design.
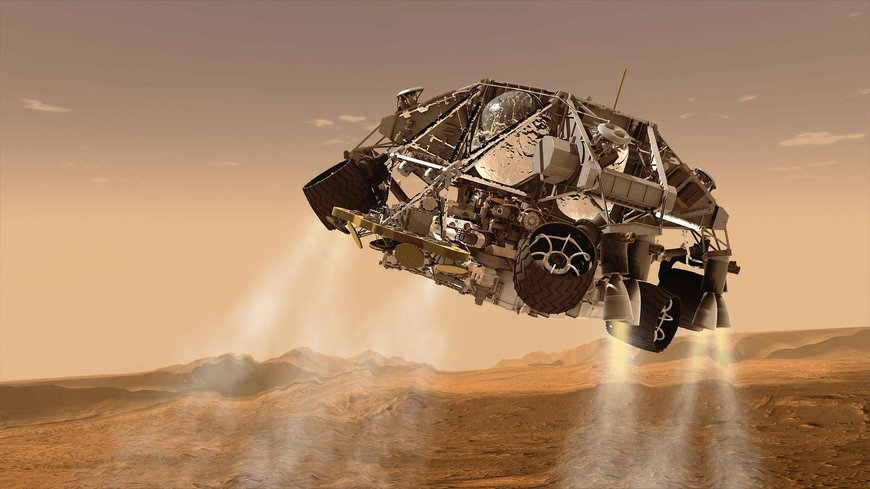
From the first successful Mars Rover mission in 1997, DC motors from maxon have been used in most successful robot missions to the Red Planet. Here Andrew Gibson, aerospace sales engineer at precision drives and motor specialists maxon UK, discusses the secrets behind maxon’s success, and explores what it takes to make motors that can thrive in the challenging environment found on Mars.
There are more than 100 of maxon’s drives already on the Red Planet and more are set to land with the Perseverance Rover, carrying the helicopter drone, Ingenuity, which will perform the first flights on Mars. maxon's precision motors and gearheads will be used to power the small robotic arm in the rover that moves valuable samples from station to station. Furthermore, Ingenuity’s direction of flight will be controlled by six 10 mm micromotors used to control the tilt of the rotor blades.
When it comes to missions to Mars, every move has to be just right, and every step must be well documented. If one of the drives fails, the entire mission is at risk. That’s why maxon’s engineers work closely with specialists at the Jet Propulsion Laboratory (JPL) to design and supply the perfect drives for the Mars Missions.
It was known from previous work that maxon’s commercial motor designs usually require some modifications to allow reliable operation in a Martian environment, particularly the wide temperature range cycling, increased vibrations and vacuum exposure. Commercial designs were analysed by a team incorporating both JPL and maxon personnel with the intention of optimising the design for use in the harsh Martian environment.
For a standard maxon catalogue flat motor to survive the requirements of the Mars 2020 mission, several changes were needed. The printed circuit board (PCB) material was changed from a flex print to FR4, a material commonly used for space missions because it does not significantly outgas, is robust enough to support the Hall sensors in a vibration environment and fulfils IPC-A-600 Class 3 requirements and testing required by JPL. The bearing preload architecture was modified so that the entire system was pushed to a hard stop, meaning individual parts would not shift on impact or as a result of vibration. A more robust spring was selected with shim ends to better distribute forces and prevent the shim from breaching the bearing.
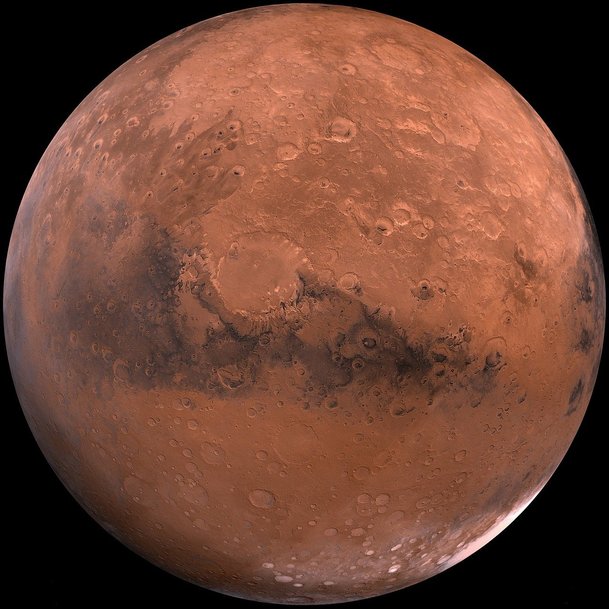
The GPX UP series planetary gearbox
The unique demands and design challenges associated with the aerospace industry have also led to the development of maxon’s GPX UP series planetary gearbox. The GPX UP series has been developed for applications that demand extreme torque and power output, smooth back drivability and high efficiency in the smallest possible volume.
Initially, design concepts for the GPX UP series were developed for the ESA’s Mars project, ExoMars and NASA’s Mars 2020 project. These Rovers were required to be highly efficient, with extreme torque and power, all while being exposed to extreme environmental conditions.
A key advantage of the new gearbox design is its high efficiency compared with traditional options. In traditional planetary gears, the planet wheels/gears rotate on greased steel or ceramic pins. However, in UP-gearbox construction, this frictional interface is replaced with needle bearings. This innovation transitions the planet gear-to-pin contacting surfaces from ‘sliding friction’ to superior ‘rolling friction’. The result is planetary wheels that rotate on smooth-running bearings; increasing efficiency, dramatically lowering generated frictional heat energy and prolonging lubricant life.
The maximum efficiency of the GPX UP series is approximately 90 per cent, roughly 20 per cent more than a standard construction gearhead and equivalent gear ratio. The increased efficiency results in an assembly capable of producing 30 per cent more torque and power. As a result of the reduced input torque need, the motor is less taxed and worn, which results in a longer system lifetime.
In summary, the new GPX UP planetary gearbox offers higher power and peak torque output, unsurpassed efficiency and an unrivalled service life. When Ingenuity takes flight, maxon will once again be part of a great engineering achievement on Mars.
www.maxongroup.com