electronics-journal.com
24
'21
Written on Modified on
Automation in manufacturing connectors
Walking through a highly automated connector facility.
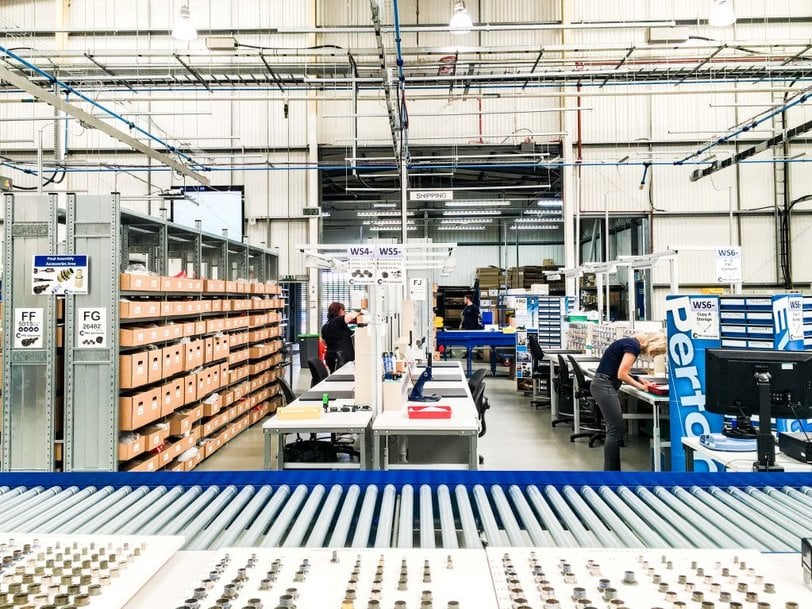
Automation underpins the modern world, but just how much of a role does it play in the manufacture of cable connectors? Here Mark Bailie, European Operations Manager at cable and connector specialist PEI-Genesis, walks us through the company’s highly automated facility in Southampton.
A connector is a term used to describe the assembly of components that make up the plug, or receptacle, at each end of a cable — and provide an electrical or signal connection.
Connectors make up the ends of everything from HDMI cables and USBs to advanced medical, aerospace and military-spec cables, such as the standard 38999 system that was developed in the 1970s for military use.
A typical cylindrical connector assembly is made up of four components: the shell, the insert, the contacts and accessories. The shell forms the outer cover that adds strength and houses the other components. Inside this sits the insert, an inner core made from neoprene rubber that holds the contacts.
As well as structurally protecting the contacts, the insert provides the dielectric, or insulating, property that allows electricity to flow from the wire in the cable, through the contacts without short circuiting. The contacts come in either the shape of a pin or a socket.
Accessories are application specific, but can include a backshell to relieve strain and prevent snagging, or to provide electromagnetic shielding. They also include clamps that allow the cable to be mounted, and protective caps. Cables can sometimes also include a coupling nut to the outer housing to hold the mating pair together, and grommets that bookend the insert and add moisture sealing.
All this goes to show that assembling a connector is not a process that’s very easy to automate. Indeed, walking through our factory in Southampton, it’s easy to forget that, in the recent past, this process would have been manually intensive and required operators to carefully assemble the components by hand.
Before automation, an operator would have sat at a fixed station, hand gluing the insert, using a press to put it inside the shell, visually checking its orientation and rotating it by hand as required. The operator would have manually glued and loaded the contacts into the insert and applied the identification marking to the shell by hand, before using a static oven to cure the connector and manually monitor temperature and duration. The final assembly and packaging would also be done by hand.
Today, our highly automated system runs on the principles of Kanban. The process starts with our manufacturing resource planning (MRP) system. Our components are vertically stored in zones, with the most frequently ordered components being situated in a zone closest to the assembly line. Our picking team then places the latest orders at the start of the assembly process.
From here, the product travels through the different stages of assembly. This is made up of pneumatic machines that bring the shell and insert together, automatically checking the alignment and rotating the inserts.
In the next stage, thousands of contacts are placed in a bowl-fed racking and gluing machine. As they come out onto a rail, the machine automatically picks and glues the contact and places it into the holes in the reel.
The next stage sees the glued contacts installed into the insert using the contact loader machine with the correct height and orientation. Some inserts can take up to 80 contacts. It can even place different sized contacts into the same insert for connectors that have varying contact sizes and arrangements.
Components are then marked using Videojet inkjet markers or laser marking dependent on the connector requirement. The glue curing process now happens in a tunnel conveyor oven where the speed and duration are automatically adjusted based on the product’s needs.
Beyond this, the finished connector undergoes quality checking, the accessories and protective fittings are added, and the product is bagged and packaged before it is dispatched.
PEI-Genesis has four automated facilities across the world and holds around 90 million components. This highly automated process allows us to deliver products within two days with a minimum order quantity of just one.
www.peigenesis.com