electronics-journal.com
05
'21
Written on Modified on
Yamaha Motor Releases New i-Cube10 (YRH10) Hybrid Placer
Complete redesign yields 50% greater mounting accuracy and production capability than previous models.
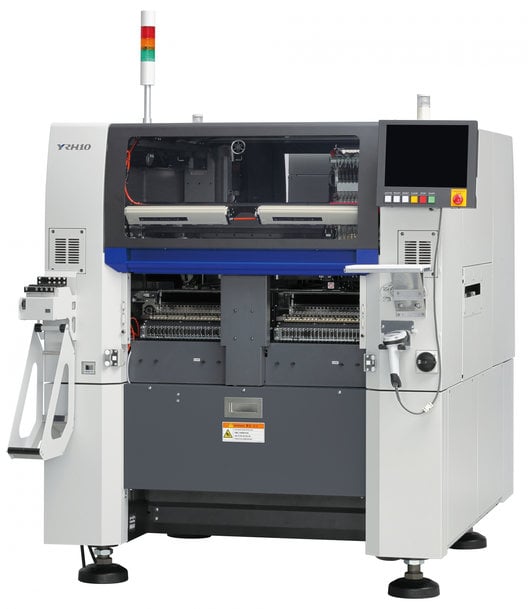
Yamaha Motor Europe, SMT Section will release its new i-Cube10 (YRH10) hybrid placer on July 1, 2021, which has both surface mounter functions for electronic components and a die bonder for wafer components.
The i-Cube10 (YRH10) was developed as the successor to the long-selling i-CubeIID (YHP-2D), known for its space-saving design as well as excellent productivity and versatility with its hybrid placer for device assembly and a wafer feed unit as standard equipment. The new i-Cube10 (YRH10) retains the same high processing compatibility suiting a wide range of electronic components and semiconductor packages, but boasts 50% higher production capability and mounting accuracy, achieving a bare chip mounting speed of 10,800 CPH from wafer supply and a mounting accuracy of ±15 μm.
Main features include 1) high-speed productivity by optimizing recognition camera operations for the mounting head and wafers, component recognition via the head-mounted scan camera, the adoption of a 10-unit multi-nozzle mounting head, and accelerated wafer swaps; and improved mounting accuracy by adopting a high-rigidity conveyor, axis control optimization, a heat compensation feature and more, 2) high versatility that allows mounting of surface mount devices (SMD) as well as wafer components with a single unit, and 3) user-friendly-focused features such as a wafer pickup condition setup utility that can optically set conditions for wafer parts, a newly developed user interface with improved usability, and a feeder unit capacity twice that of previous models.
Market Background and Product Outline
At the worksites for mounting electronic components and semiconductor packages in recent years, the trends of making things smaller and thinner, lowering power consumption, achieving higher functionality, and greater diversification are accelerating rapidly, and the implementation of even more delicate processes is progressing. In turn, the market is now looking not only for higher mounting accuracy than ever before, but also improved productivity, which directly influences packaging costs.
The newly developed i-Cube10 (YRH10) represents the first redesign in 14 years—since 2007—and is a swift response to the above changes and demands in the market, achieving a 50% improvement over previous models in both mounting accuracy and productivity. With the ability to mount various types of components such as surface mount devices and wafer components with a single unit, we aim to further bolster our sales in the electronic component and semiconductor package markets.
With our unique 1-Stop Smart Solution concept, we take advantage of being the industry’s leading manufacturer with a full lineup of SMT equipment—from SMD storage, solder paste printers and glue dispensers to surface mounters and AOIs—and to create smarter factories, we will offer new value via the high-level integration and coordination among our line equipment that removes the need for black boxes.
Product Features
1) High-speed, high-precision mounting
Operation of the mounting head and wafer camera has been optimized, eliminating all standby time loss of the mutual units. In addition, by equipping the head with a scan camera, component recognition following wafer picking is completed during movement and taking the shortest path to the mounting position becomes possible, creating an efficient operations cycle. Further, the number of nozzles on the mounting head has been increased from 4 to 10, drastically reducing of the number of head cycles needed per number of components to be mounted. Thanks to these features, the i-Cube10 (YRH10) achieves a high bare chip mounting speed of 10,800 CPH (when supplying wafers).
The wafer replacement time has also been shortened, and even multi-die products requiring frequent wafer replacement can be produced without reducing throughput. This unit also aids in achieving high-quality production by effectively utilizing our recognition system for ball/bump components, refined through the development of our flip-chip bonders such as the YSB55w.
Additionally, the rigidity of the frame was extensively reviewed. A high-rigidity conveyor was adopted to reduce its dynamic vibration during head operation and optimization of axis control parameters, a heat compensation feature and more achieve and maintain the unit’s high mounting accuracy of ±15 μm (μ+3σ).
2) High versatility
Since various types of components such as surface mount devices and wafer components can be mounted with the i-Cube10 (YRH10), a single unit can be used for mounting operations instead of having to divide tasks among multiple devices as was required before. This reduces costs and installation space.
The unit is also equipped with a variety of functions facilitating its high versatility, such as a non-stop wafer feed unit that can set up to 10 wafers, compatibility with PCBs up to L330 mm × W250 mm in size, automatic tool replacement, and a dual push-up unit.
In addition, the i-Cube10 (YRH10) is also compatible with the auto-loading feeder Yamaha surface mounters are known for, and can always supply tape reel components without stopping production or requiring supply timing selection.
3) Easy operation
The wafer pickup condition setup utility can visually set conditions for wafers, making the task require little to no skill and further supporting operator work efficiency. In addition, the i-Cube10 (YRH10) is packed with user-friendly features, such as a newly developed user interface with improved usability and a feeder load capacity twice that of previous models.
www.yamaha-motor-im.de