electronics-journal.com
18
'21
Written on Modified on
The Evolution of Pressure Sensors that Enable “Smart” Factories
With awareness of environmental issues growing, choosing products and services with the least possible environmental impact has become the norm.
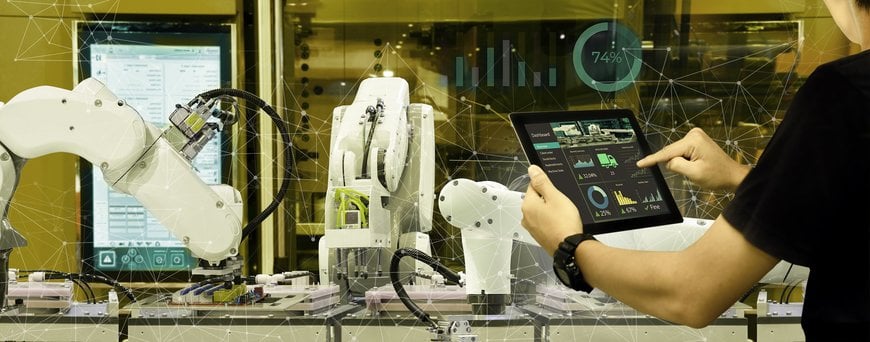
Efforts to reduce the burden placed on the environment by the manufacturing of products are also drawing attention. At “smart” factories, which aim to increase production efficiencies by leveraging the latest digital technologies, many sensors are being utilized to collect a variety of data from manufacturing facilities and equipment.
Life Cycle Assessment evaluates the environmental impact of manufacturing sites
From personal lifestyles to corporate procurement of materials and parts, Green Purchasing/Green Procurement *1 initiatives—which promote choosing products with less environmental impact—are expanding. There is also a renewed interest in the concept of Life Cycle Assessment (LCA) *2, which is an effort to evaluate the environmental impact of a product throughout its life cycle, from procurement of raw materials, manufacturing, distribution, disposal and recycling, to its environmental performance during use.
The concept of LCA is said to have originated in the 1960s, when a U.S. beverage manufacturer conducted a study on the environmental impact of returnable bottles (glass bottles that can be washed and reused) compared to disposable, one-way containers. Although returnable bottles inure the cost of collecting and washing the bottles, they were determined to have a lower overall environmental impact over one-way containers—which are discarded after a single use—because there are no additional manufacturing resources expended with returnable containers.
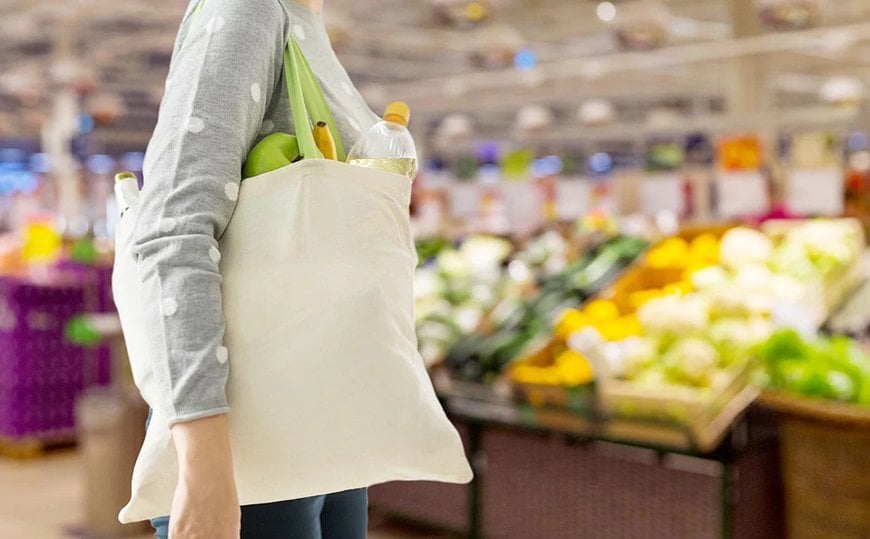
According to a survey on industrial CO₂ emissions, manufacturing accounts for about 25% of CO₂ emissions across all industrial sectors (Source: National Institute for Environmental Studies, Japan). In the effort to achieve carbon neutrality throughout all industries, reducing energy consumption at manufacturing sites is a considerable challenge. Renewable energy sources like solar and wind power are expected to help reduce CO₂ emissions from factories. “Smart” factories are also expanding in many countries.
“Smart” factories aim to improve efficiencies in the manufacturing industry
Factories and plants have been using factory automation (FA)—such as automated machines and robots—to increase production efficiencies by making them unmanned. The latest smart factories take these efforts to the next level, optimizing the entire factory by making full use of data gathered from machines and equipment.
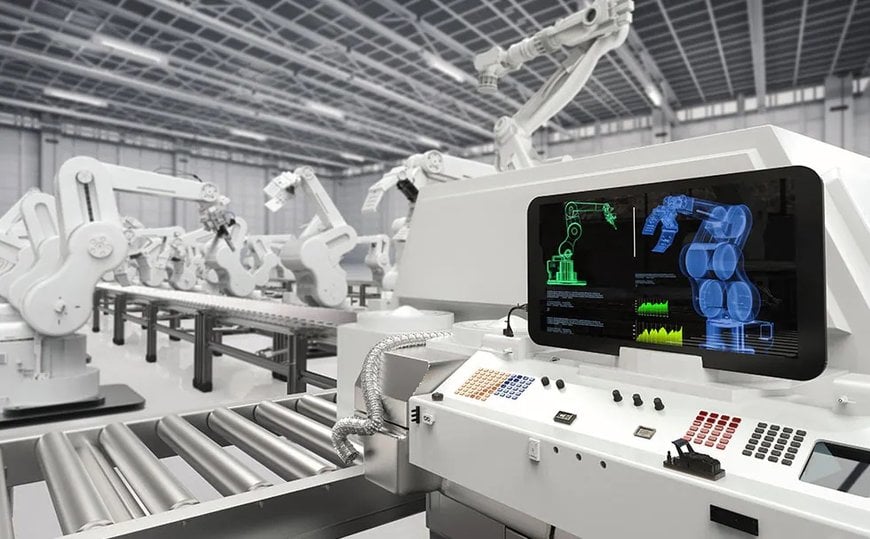
In a smart factory, a variety of sensors enable the real-time monitoring and operational management of manufacturing equipment, systems, pumps, motors and other devices, as well as the oversight of facilities and movements of workers. This has a preventative effect on machine malfunctions, improving product quality and productivity. Additionally, the data collected can be aggregated and analyzed to optimize operations even further. To implement this type of DX (Digital Transformation) in manufacturing, it is essential to have a variety of sensors, such as small, high-precision pressure sensors and transmitters with networking capabilities, that can be installed across various factory equipment and devices.
Creating a compact, high-precision MEMS pressure sensor
Factories use a wide variety of liquids and gases to drive equipment and produce products, such as air compressors, machine tools powered by hydraulic cylinders, and cleaning equipment utilizing high-pressure water. By using sensors to accurately monitor and control the pressure of these liquids and gases, unnecessary energy consumption can be reduced, leading to improved production efficiencies and product quality.
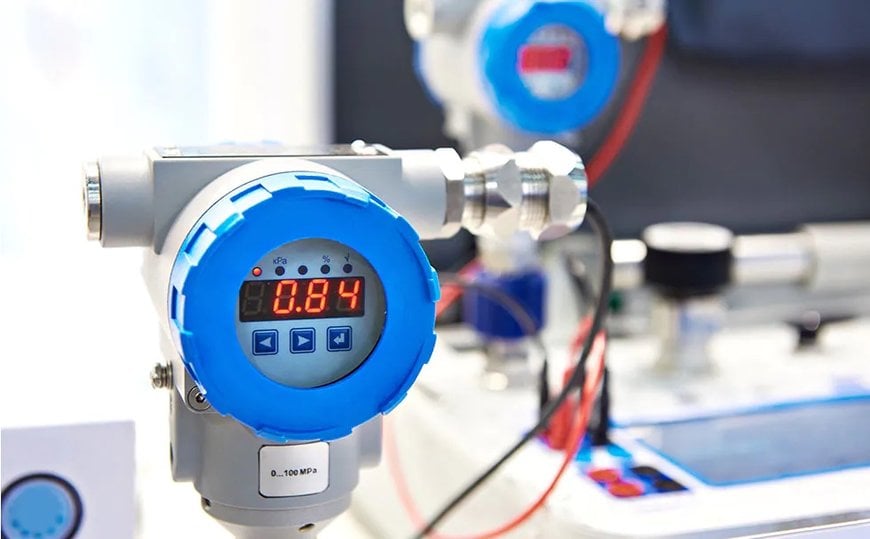
TDK has created a compact MEMS pressure transmitter, which integrates a high-precision piezoresistive sensor in a package that is only 6 mm thin. With a footprint as small as 24 by 26 mm, it offers an exceptionally high accuracy of just ±1% FS (Full Scale) across a temperature range of -25° to +85°C. The device is also equipped with a connector that allows multiple sensors to be daisy-chained, enabling the sensing of multiple devices on a single network.
The MiniCell® series of miniature differential pressure transmitters, which are particularly well-suited for applications in harsh environments, can operate in temperatures ranging from -40° to 140°C. It delivers a high accuracy of less than 1.5% FS over the entire temperature range and product life. Its stainless steel diaphragm construction enables the pressure measurement of aggressive liquids and gases. It can be used in a wide range of industrial applications, including the measurement of highly corrosive materials such as automotive exhaust gases and fuels.
TDK offers a wide range of high-precision piezoresistive pressure sensors that measure absolute, gauge and differential pressures. They are being utilized in a multitude of applications, including industrial, automotive and medical equipment. The broad lineup of sensor solutions contributes to the digitalization of manufacturing sites, the reduction of CO₂ emissions, the alleviation of labor shortages through automation, and other initiatives beneficial to society.
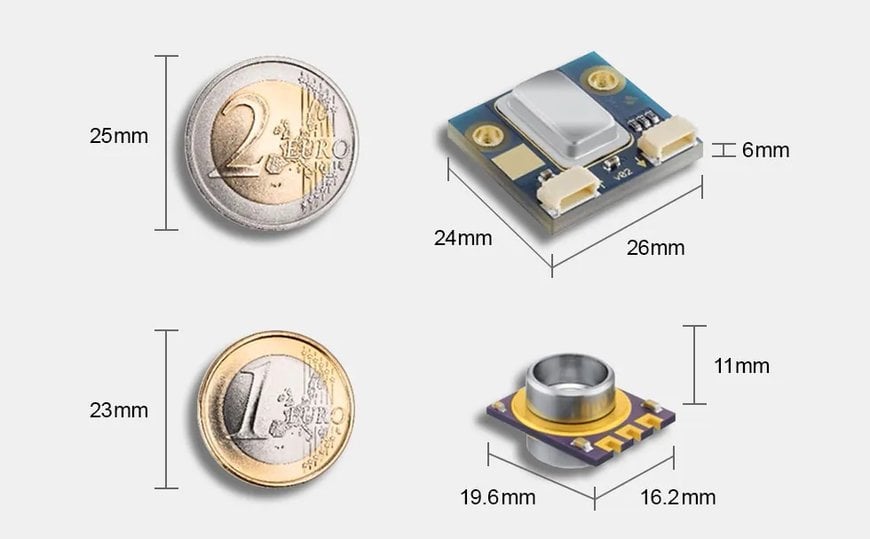
The new B58621V series of pressure sensors—designed explicitly for use in smart factories—is compact, highly accurate, and provides long-term stability. The MiniCell® series of compact pressure sensors is suitable for a wide range of industrial applications, especially those in harsh environments. For more information about TDK products, please visit the Product Center.
www.tdk.com