electronics-journal.com
17
'21
Written on Modified on
The importance of signal conditioning in industrial processes
Almost 150 languages are derived from Latin. But despite similarities in form, differences in letter combination mean this isn't sufficient to enable interlanguage comprehension. The same goes for processing plants; converting signals generated in the plant into an understandable form for control systems is a challenge. The answer? Signal conditioning.
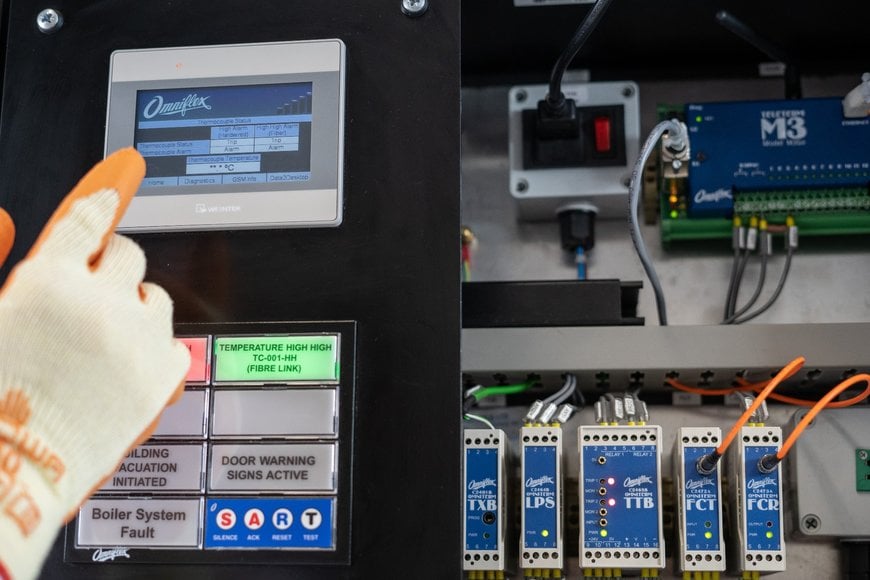
Here Ian Loudon, international sales and marketing manager at signal conditioning specialist Omniflex, explains why signal conditioning is industry’s Google Translate.
Processing plants often produce analogue signals in their thousands per minute, directly from sensors embedded in the process including those for temperature, pressure, flow and any other physical parameters required for control and monitoring. This data can be analysed to trigger actions that keep operations flowing efficiently and safely. This is done by feeding information into a control system or by triggering an alarm annunciator in safety critical applications that alerts operators in the event of an emergency.
Mixed signals
Signal conditioning is a crucial process in plants, which involves preparing analogue signals to be converted and scaled for further processing for control and monitoring. Before a data acquisition device can measure the signal, a signal conditioning unit is required to put the data into an understandable and universally accepted form. One challenge is scaling small physical signals such as mV or even µV to a standard plant signal that can be used for control.
Signal conditioning is also essential to avoiding interference and erroneous data. In processing plants,electromagnetic noise and ground loops and signal isolation issues are problematic to PLCs, SCADA and DCS that run the plant. If input data is incorrect, this can adversely impact the industrial processes that rely on it. For safety critical applications, like nuclear and petrochemical plants, ensuring this data is as accurate as possible is not an option, but a necessity.
Unfortunately, noise and ground loops are common. Two devices that are connected within the same circuit butgrounded in different locations can result in a difference in potential. This difference can lead to a flow of electrons, which generates a loop current known as a ground loop. Since the ground loop runs along the same wires as the analogue signal that the control system needs to accurately interpret, it can interfere and produceerroneous data.
Clear conditioners
Mitigating the potentially catastrophic impact that erroneous signals can have on industrial processes is a task assigned to signal conditioning units. By taking signals from sensors across the plant, the signal conditioner is responsible for converting the input signal into the desired output signal, the most common being 4-20 mA.
Typically, a different signal conditioning module is required for each input signal. So, plant managers could require several different units, and replacements, for each signal in a plant, which is both complex and expensive. However, Omniflex’s Omniterm TXB Universal Input unit can eliminate this complexity.
The Omniterm TXB unit has dip switches on its sides, which allow operators to set the input and output signals as required, meaning just one type of module is needed to process a range of different signals from various applications. It also means that less stock is required, as the same replacements can be used with all input signals, making for more cost-effective and streamlined inventory management.
For signals being collected from harsh or hazardous areas, IECEx and ATEX certification is provided, verifyingthat the unit has been fully tested and is approved for use in hazardous or explosive atmospheres. It also has been independently tested for IEC61508 SIL-1, which certifies that the unit can be used as part of a plant safety system when required.
Since TXB is pre-certified and universal, Omniflex can speak directly with engineers and analyse system data to create a signal isolation solution for any application. The high quality and broad suitability of the TXB alsoreduces the time required for installation and validation, allowing Omniflex to solve a plant’s signal issues efficiently and quickly.
Like languages, getting just one element wrong can change the entire meaning of a signal, which can create a muddle of detrimental machine misunderstandings. But like Google Translate, signal conditioners are the hero at hand, translating these signals and disregarding inaccuracies to ensure clear communication for safe, efficient operations.
www.omniflex.com