electronics-journal.com
15
'22
Written on Modified on
Build or buy a three-axis motion controller?
Gerard Bush of motion specialist INMOCO compares the build versus buy approach for PCB-motion controllers. Three-axis embedded PCB motion controllers are integral for applications such as robotic arm control.
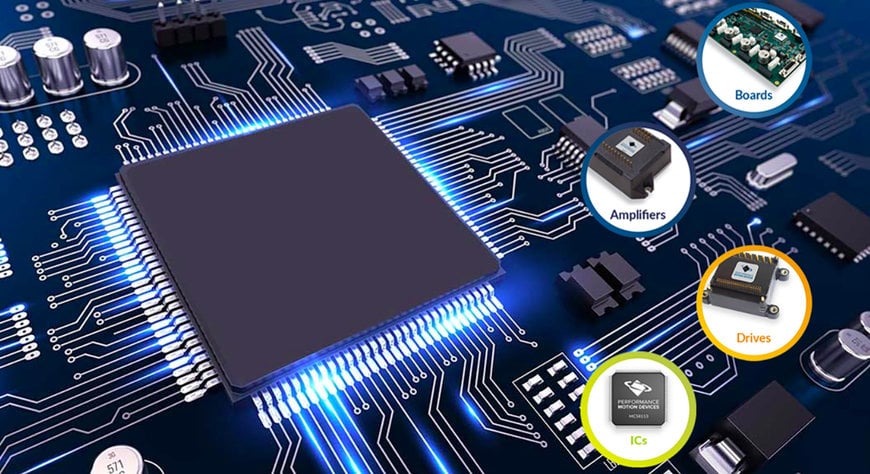
While high volume and specific development needs might drive towards an in-house build, minimising development time and lowering cost for smaller volumes is an advantage of buying-in a controller. Comparing these approaches, a hybrid option can also offer the best of both worlds.
Printed Circuit Board (PCB)-based motion controllers are frequently integrated within applications such as laboratory automation, mobile robotics, test equipment, packaging machines, and robot arm control. Typically controlling three axes of brushless DC and/or stepper motors up to around 350W, the increasing trend is to embed a microchip-based controller within the machine itself. The close proximity this provides enables faster response times, less noise, and a more compact footprint, plus a reduced cabling.
Balancing specification requirements with cost, an OEM faces the decision of procuring an established controller or developing their own. Assuming an off-the-shelf controller can meet needs, development volume that impacts the total procurement cost might be the deciding factor. Alternatively, an exacting specification might drive internal development. While examining the pros and cons of both approaches, a hybrid option can combine the best of both worlds.
Building a controller
The advantages of developing in-house are two-fold. Firstly, this approach gives a controller that is entirely tailored to the application in terms of connectors and form factor, as well as dedicated functionality. Unique design can also be a selling point, providing it includes features that the market is willing to pay for. The other main advantage is cost. Assuming the production run is high enough, talking in the region of 1,000 units or more, a custom designed controller might be a more cost-effective procurement option.
The clear requirement, however, is the need for expertise and time in development. While cost can be saved compared to high-volume procurement, the design effort for developing a three-axis motion controller PCB is significant.
Selecting connectors and the wiring scheme is a preliminary step, and this stage can take up to three months. Next, a pivotal decision is the approach to the motor amplifier. A designed-from-the-ground up amplifier offers the greatest flexibility in specification and control. However, with design considerations such as electromagnetic interference and current control, this process is likely to take at least three months or more. Instead, an off-the-shelf PCB-mounted amplifier can be integrated, still providing advanced features such as safety controls, while saving development time.
The other primary component decision is the motion control chip itself. Using a separate micoprocessor gives the freedom to write a customised motion engine code. This affords complete flexibility over motion functions, but development would add at least 12 months to the project. To enable communication with the host network and coordinate motion sequences, microprocessor system software code development is also required, taking up to six months.
Like the approach to the amplifier, alternatively an off-the-shelf motion control chip can be integrated into a custom-designed PCB controller to save time. This would give the OEM control over attributes including the PCB’s form factor, while still providing motion capabilities such as profile generation and field oriented control.
Progressing to the PCB schematic, this stage requires research, selection, and testing of components to achieve the circuit. Integrating the control chip and amplifier, the latter would also require a dedicated circuit. In total, at least 12 months should be allowed for PCB schematic development.
The final aspect of the software development process is application and motion parameter development. The timespan depends on previous application development experience but can take from 12 to 16 months. However, whether the motion controller is an in-house build, a buy-in, or a hybrid design, this stage of motion control development is a prerequisite.
With an estimated total of 34-58 months’ work, divided into a three-person team this project could take up to 18 months or more. Notwithstanding the design effort, for some OEMs, the long-term advantages may be worth it.
Buying-in a motion controller
All of these steps, except for the application and motion parameter development, can instead be removed by using a ready-to-go PCB-based motion controller. This effectively reduces development time to a little over a year and doesn’t necessarily mean a sacrifice in motion control features. As well as functionality such as profile and servo position control, integrating user downloadable code written with C language libraries also extends their control flexibility.
An advantage of buying-in an off-the-shelf motion controller is that it can also be more cost-effective if a lower volume is required. Perhaps up to approximately 1,000 units, integrating a pre-developed controller could be the less expensive option. If your organisation doesn’t have the existing development know-how in house, this approach could also save significant cost in hiring the required expertise.
Quicker development also means faster time to market. Demands of end users and the competitive landscape, might make this the preferable approach, even for higher volume projects.
Hybrid PCB-motion control development
Now, it’s possible for OEMs to use a hybrid approach that features PCB-mounted motion control modules. These single-axis modules can handle up to 1kW and can execute user-written application software, extending control flexibility.
Just like an off-the-shelf controller, these modules include advanced motion functions such as profiling, field oriented control, and safety. The advantage though is the ease and speed of integration. Mounted on a user designed, application-specific interconnect board, these modules require much simplified wiring, needing just connectors and capacitors.
Like the buy-in option, the engineering resources required are significantly lower. Following simplified hardware integration, engineers can move directly to application development. This approach however still lets the OEM create a controller within their own form factor. Given the right volume, procurement cost of the hybrid approach can also return a lower rate than the buy-in option.
Making the choice
To navigate priorities in design, INMOCO’s engineers can interface with OEM development teams, providing insights to clarify the right approach. INMOCO works alongside Performance Motion Devices, a motion control manufacturer that has innovated the embedded PCB motion control concept. Whether the application requires a build-from-scratch, buy-in, or hybrid approach, INMOCO and Performance Motion Devices can provide the optimal control solution.
www.inmoco.co.uk