Sensor Innovations Revolutionize Gas Leak Detection Technology
Methods for detecting gas leaks have been relatively stagnant over the last four decades, with the options consisting of older pellistor/catalytic bead sensors or non-dispersive infrared (NDIR) sensors.
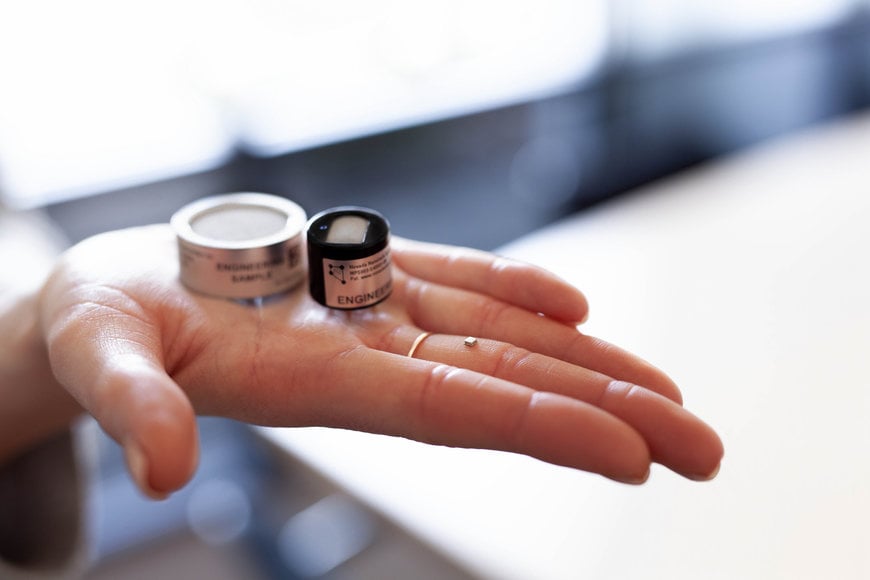
But each of these sensors has limitations, which, until recently, impacted the operator's ability to detect harmful gases reliably.
Recent innovations in sensor technology make it possible to overcome these limitations. The Molecular Property Spectrometer (MPS) is a new type of sensor that enables more accurate and reliable gas detection than has ever been possible.
How It Works
The MPS uses a micro-electromechanical system (MEMS) transducer to measure a change in the surrounding air and gases' thermal properties. The output reading contains multiple indicators and environmental data that currently can identify 15 different types of gases and their concentration in the vicinity for up to a year, providing TrueLEL readings after one calibration.
In addition, their overall life expectancy can be up to five years – far longer than either pellistor or NDIR sensors.
This capability has never been possible in the past while using pellistor/catalytic bead sensors or NDIR sensors, both of which can accurately detect only one gas.
MPS Sensors Can Deliver Accurate Measurements For Multiple Hazardous Gases Automatically.
In comparisons with both pellistor/catalytic bead sensors and NDIR sensors, the MPS has distinct advantages and, in most instances, eliminates the shortcomings of both.
Pellistor/Catalytic Bead Sensors and MPS Sensors
Pellistor, or catalytic bead sensors, have been in use for nearly a century. Their primary appeal is their low cost and the fact that they are sensitive to nearly all hazardous gases, including hydrogen, methane, butane, propane, and carbon monoxide, among others.
But it is essential to know how these sensors work to understand where they are vulnerable. The sensors measure temperature differences between two beads – an inert one and one coated in a chemical catalyst. As an internal heater raises the temperature within the sensor, the bead coated in catalyst heats more than the inert one if they are in the presence of a flammable gas. The difference in temperature allows the sensor to provide a reading related to the concentration of the hazardous gas being measured.
Unfortunately, they are prone to "poisoning," which means that the sensors become inoperable when exposed to high concentrations of flammable and combustible gases, or even very low concentrations of common gases like chlorine, silicones, and acidic gases. This is a significant disadvantage as it can result in inaccurate readings. This poses a potentially grave danger as the sensor appears to be working normally. This puts the user in a very dangerous situation when what they believe is an operational sensor fails to alert them of hazardous conditions.
And while pellistor/catalytic bead sensors respond to a full range of flammable gases, their readings are only accurate for the single gas they have been calibrated to detect. Nearly all other readings for other gases will be inaccurate. In addition, these sensors do not function in low-oxygen environments, require high amounts of power, have a limited life expectancy (about two years), and must be calibrated frequently.
The MPS sensor, on the other hand, is not prone to poisoning, and if in the rare instance it becomes inoperative, it will alert the user through its fail-safe and built-in diagnostic capabilities. This helps avoid a dangerous scenario. The MPS sensor can detect the full range of flammable gases virtually instantaneously to deliver an accurate reading of individual gases or gas mixtures. In addition, the MPS sensor lasts up to 5 years and never requires recalibration. It uses less power and provides automated environmental compensation.
This features comparison shows that the newer MPS sensor technology eliminates or mitigates the deficiencies commonly found in a pellistor/catalytic bead sensor. Taking it a step further, the advanced MPS sensor bettered the pellistor/catalytic bead sensor in performance testing.
The performance of both sensors was tested when calibrated to methane, then exposed in sequence to 50 %LEL concentrations of methane, hydrogen, and butane. The following are the documented results.
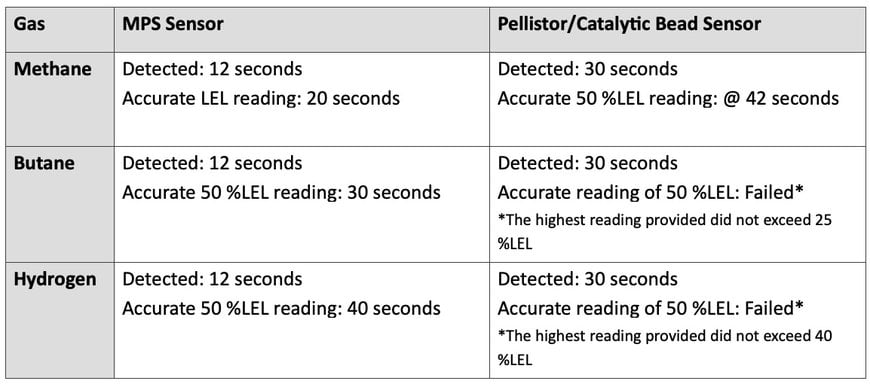
The MPS sensor performed better than the pellistor/catalytic bead sensor across the all three gases, delivering a more accurate measurement faster.
Non-Dispersive Infrared Sensors (NDIR) and MPS Sensors
The non-dispersive infrared sensors, or NDIRs, were introduced and became popular for use in gas detection in the 1960s. NDIRs use infrared light, which is absorbed at certain wavelengths by hazardous gases. By measuring the intensity of the light transmitted through a sensing chamber containing gas and comparing it to a reference, the instrument can determine the concentration of hazardous gas present.
NDIR technology represented a huge leap in gas detection technology 40 years ago. Today, like pellistor/catalytic bead sensors, these sensors use dated technology that has serious limitations. The most significant is that they cannot detect hydrogen, since it does not absorb infrared light. Hydrogen is commonly found in the mining and petroleum industries, and can be incredibly dangerous. Allowing it to go undetected may create hazardous working conditions. NDIR sensors can be calibrated only to a single gas, making them ineffective at detecting gas mixtures.
NDIR sensors are also very sensitive to environmental changes. Moderate fluctuations in temperature or humidity can freeze the output reading, leaving the user unable to determine gas presence or concentration. Also, humidity, fog, and ambient light can cause interference with detection if they are able to permeate the open chamber. And while they need calibration less frequently than the pellistor/catalytic bead sensors, they still require calibration at least yearly. Since NDIR is a proprietary technology, it can be expensive.
MPS sensors eliminate these limitations. As mentioned, they can detect up to 15 gases accurately, including hydrogen, need a single calibration during their lifetime, and are competitively priced. Performance testing clearly shows the advantages of the new technology in the MPS sensors. As the test showed, the NDIR and MPS sensor performed similarly when detecting the methane gas to which they were calibrated. However, the MPS sensor outperformed the NDIR sensor when detecting both butane and hydrogen.
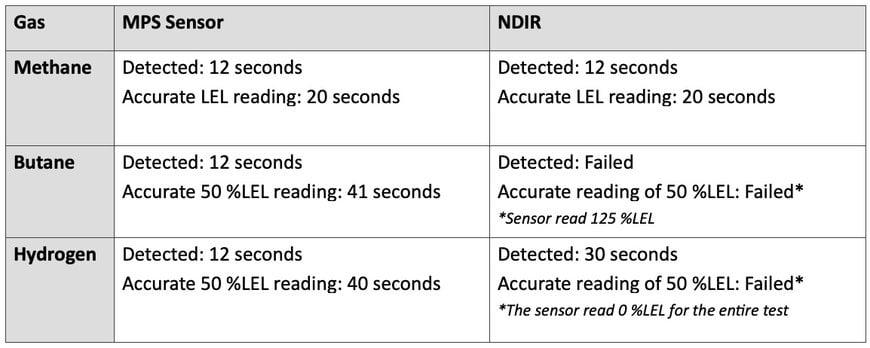
Conclusion
MSP sensors deliver a more accurate reading of multiple gases than either the NDIR or pellistor/catalytic bead sensors. Moreover, they offer many other advantages:
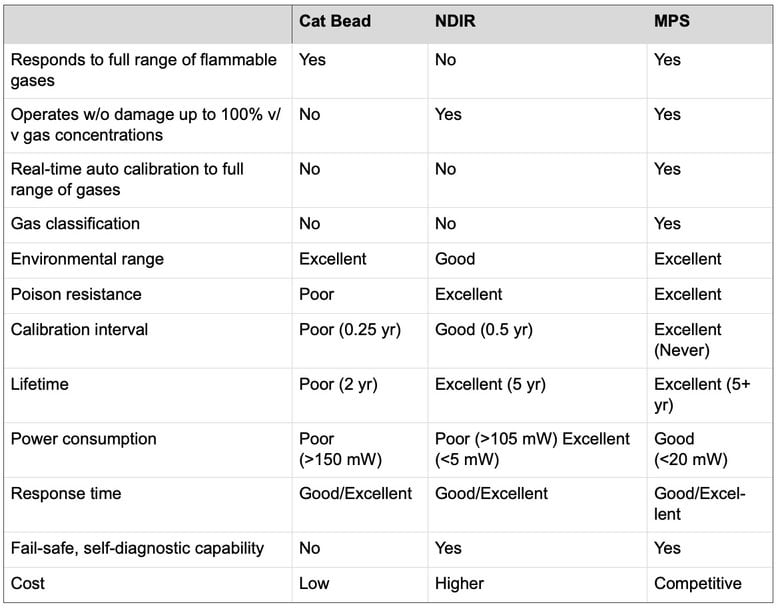
Relative performance in key categories of the three main sensor types
- Calibration: MPS sensors need less calibration than either NDIR or pellistor/catalytic bead sensors. An MPS sensor can provide stable, reliable results for up to a year, rather than every 3-6 months. They also offer real-time calibration, which neither the pellistor or NDIR sensors are able to do.
- Environmental Variations: MPS sensors are accurate even if there are rapid changes to temperature, pressure, or humidity. They detect gas presence and concentration across a wide range of environmental conditions, from -40C to 75C and from 0% to 100% relative humidity.
- Impervious to Poisoning: Unlike pellistor/catalytic bead sensors, MPS sensors do not drift, decay, or poison. They also alert users immediately if the sensor is faulty or malfunctions.
- Cost: The MPS sensor is competitively priced, requires no maintenance, and never needs calibration, further lowering its overall total cost of ownership.
MPS gas leak detection sensors are the next generation of combustible gas detection and set a new standard in performance, reliability, accuracy, and value. Not only do they represent a tremendous leap forward from NDIR and pellistor/catalytic bead sensing technology, but they help companies maintain a safe work environment, protect the environment and realize operational efficiencies.
www.nevadanano.com