electronics-journal.com
01
'21
Written on Modified on
What makes a space-worthy connector?
The special design considerations that go into connectors bound for space.
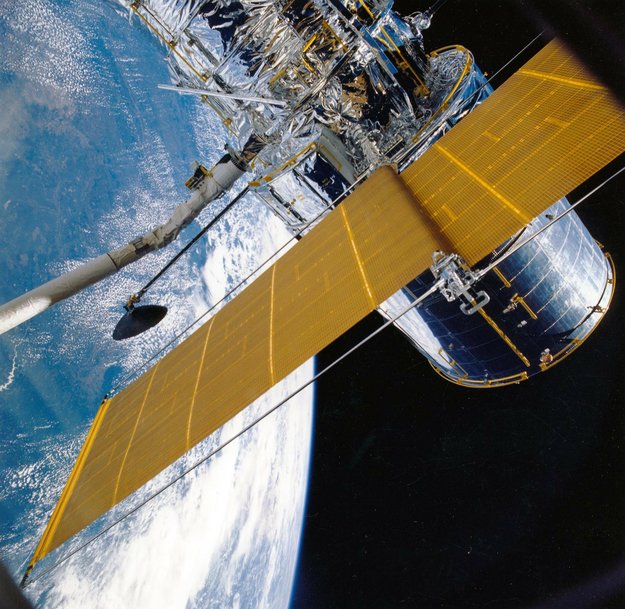
With amazing self-landing rocket boosters, deep-space asteroid hopping probes and the reignition of Moon missions over half a century on — the space race might be over, but the race to exploit the final frontier is just heating up. Here, Jonathan Parry, Senior Vice President and European Managing Director at cables and connectors supplier, PEI-Genesis, discusses the special considerations that go into space-worthy cables and connectors.
Down here on Earth, it’s easy to forget how good we have it. Just a mere hundred kilometres up, you’ll find blistering heat, frigid cold and pressures bordering on a vacuum. Even getting equipment out of Earth’s gravity-well and into space is a monumental hurdle — there are reasons why rocket boosters are the size of tower blocks, after all.
Any equipment put into space is also completely inaccessible to maintenance, meaning every little detail of design must be considered, with connectors and cabling near the top of the list. Otherwise, if something breaks, disconnects or encounters errors, you’ve effectively just launched a very big, very expensive firework.
Up where there’s no air
Every kilogram sent into space costs thousands of dollars, so saving weight is crucial. This can make lightweight plastic connectors quite attractive as they offer higher strengths at lower weights than other materials. However, plastics can encounter problems in the near-vacuum environment of space.
The problem is that many plastics degrade when exposed to vacuum, through a process called outgassing. Here the extremely low external pressure literally boils volatile compounds out of the polymer lattice.
This can have a number of negative effects. Firstly, unregulated outgassing like this strips the plastic of some of the particles that help hold it together, causing components to become brittle and directly reducing their expected lifespan. Furthermore, the cloud of loose particles condenses on surfaces inside the space vehicle, such as sensors and other equipment.
Seeing as replacing embrittled connectors and cleaning these laminated sensors would require another multi-million-dollar rocket, avoiding outgassing is crucial. The way around this is to treat the connectors before they’re launched.
At PEI Genesis this is achieved by baking its wide range of space-bound connectors in a vacuum-sealed kiln. This process gradually bleeds the volatiles from the plastic, removing any possibility of further outgassing while also preserving the strength of the material. The connectors are then closely inspected and tested to ensure they meet the stringent requirements of space, aerospace and military applications.
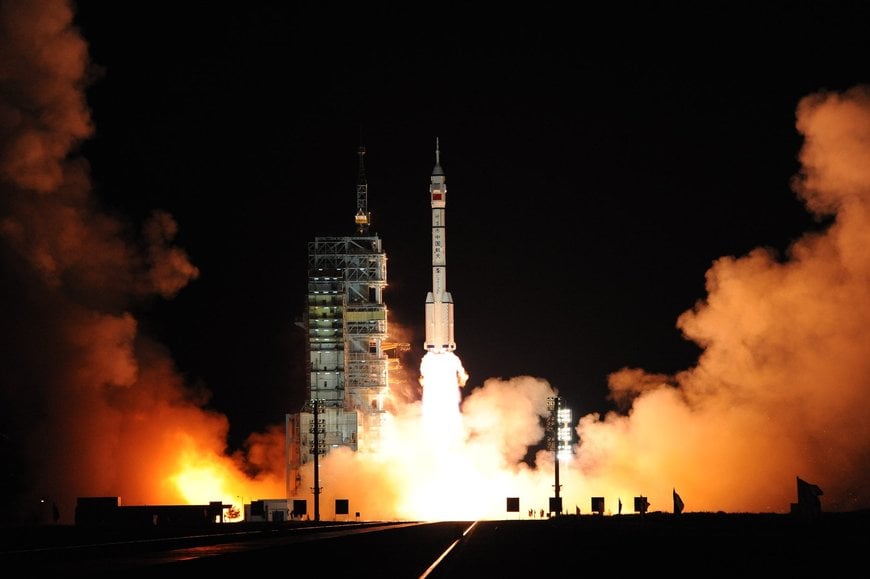
Removing residual magnetism
Unfortunately, metallic connectors can bring another problem with them — residual magnetism. This is because the permanent magnetic field affects nearby equipment, degrading performance and potentially ruining data retrieved from them.
Examples of equipment sensitive to magnetism in this way include camera charge-coupled devices (CCDs), onboard vibration sensors and accelerometers, gyroscopic reaction wheels, bimetallic thermometers and, naturally, magnetometers. Errors introduced into these measurements can turn mission-critical data into meaningless garble, and could potentially cause complete failures if left unchecked.
Avoiding residual magnetism in connectors comes directly down to the materials used. Wherever possible non-metallic connectors should be used, but metallic connectors constructed specifically with low residual magnetism include the ITT NM/NMB D Sub range. These come in a variety of metallic shell materials, from low-magnetic brass and aluminium, to specially demagnetised stainless steel. They are all tested to ensure they meet space-grade standards.
It’s not always true that what goes up must come down, but that’s half the problem if equipment performs badly or breaks while in orbit. Getting up there is a serious task, so making sure only the highest quality connectors reach the launchpad should be top of the list of design and engineering priorities.
www.peigenesis.com