Inductors: TDK develops downsized, compact, thin-film power inductors for automotive power circuits
TDK Corporation (TSE: 6762) has developed a series of thin-film metal power inductors for automotive power circuits.
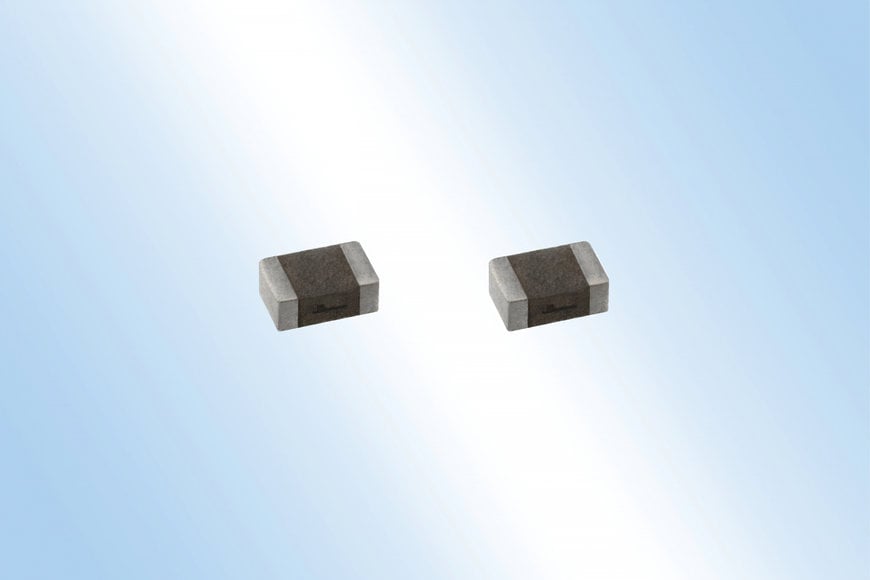
- Compact size: 2.0 mm (L) x 1.25 mm (W) x 1.0 mm (H)
- Supports an operation range between –55 °C and +150 °C
- Increased robustness against mechanical stress due to the resin electrode structure and thermal shocks
- Compliant with AEC-Q200 Rev D
The new TFM201210ALMA inductors feature a mounting area downsized approximately 22 % from TDK’s conventional product, TFM201610ALMA (2.0 mm (L) x 1.6 mm (W) x 1.0 mm (H)). Mass production will begin in August 2021.
Demand has recently increased in ECU* mounting for the electrification of various automotive controlling functions, autonomous driving, information communication and other purposes. Downsized inductors for power circuits contribute to space-saving in a mounting substrate, at a time when quick advances in ADAS** performance increase the number of components typically used in system architectures.
In addition to its compact dimension of 2.0 mm (L) x 1.25 mm (W), this series uses the TDK proprietary metallic magnetic material as its core material. The thin-film inductors support a wide range of operating temperatures from -55 °C to +150 °C, the highest level in the industry***. Moreover, it features increased robustness against mechanical stress, such as vibrations and shocks due to the resin electrode structure.
In addition to the new items, TFM series includes a lineup of products with a rated voltage of 40 V, allowing use on an automotive power circuit side directly connected with a 12 V battery.
***Source: TDK, as of July 2021
Glossary
- *ECU: Electronic Control Unit
- **ADAS: Advanced Driver-Assistance Systems
Main applications
- Automotive camera module
- Communication module for V2X
Main features and benefits
- A compact size of 2.0 mm (L) x 1.25 mm (W) x 1.0 mm (H) to facilitate space saving
- Supporting an operation temperature range between –55 °C and +150 °C (including self-heating)
- Increased robustness against mechanical stress due to the resin electrode structure and thermal shocks