What the electronics industry can learn from the automotive sector when it comes to quality measurements
The electronics industry has been under increasing pressure, with the pandemic seeing a rising demand for electrical devices as many people stay at home longer – and at the same time need to work, stay connected with loved ones and be entertained.
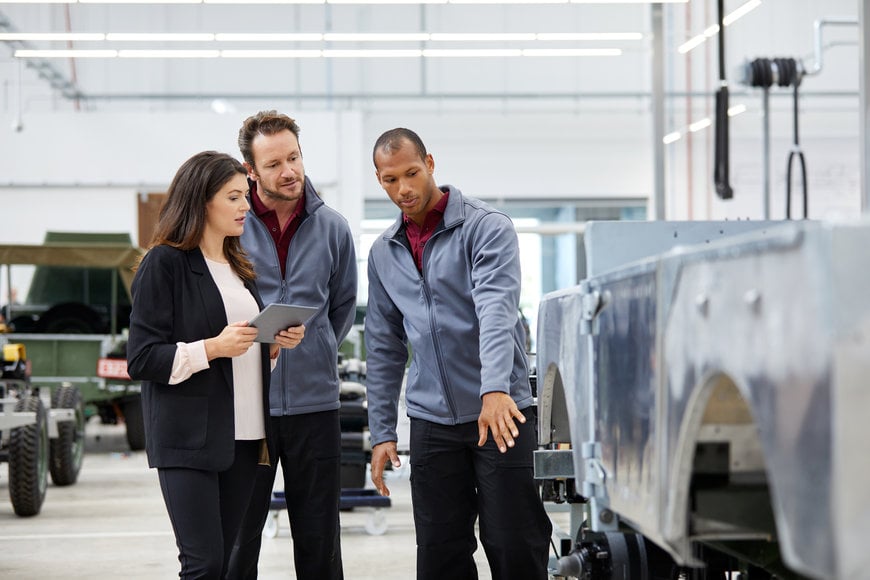
But while this may be good news for companies’ bottom-lines, it has placed an almost unprecedented strain on the industry’s manufacturing processes.
Indeed, the electronics industry is currently experiencing a computer chip shortage – the chips, also known as semiconductors, are required for consumer devices to be able to work. A boom in demand as well as Covid-impacted supply chains are just some of the contributing factors to this situation.
And to make matters worse, ensuring quality levels of the products produced is becoming harder as the speed they need to be manufactured at becomes forever faster.
What’s more, a recent, ominous survey revealed that 64% of electronics manufacturers have product quality issues; citing a number of factors that included the ever-increasing speed of manufacturing, customer demands, tighter tolerance levels and, importantly, quality metrics themselves.
Of course, if the electronics industry is to thrive then a key component to this is ensuring quality measures are as stringent as they could be. But how?
The answer lies in taking inspiration from the automotive industry and investing in Layered Process Audits (LPAs).
How LPAs can help
LPAs are proven to help prevent manufacturing escapes and cut production costs. LPAs involve regular checks of the plant’s manufacturing processes, catching mistakes in a product’s manufacturing process before it is complete. It is, therefore, important that the industry looks at adopting digital LPAs sooner rather than later.
When properly implemented, LPAs are the most effective way to ensure that processes consistently follow approved standards, reducing waste and rework, improving quality, and driving cultural change. Essentially, LPAs ensure that the approved process and formula are followed, with a heavy focus on the human aspect of the manufacturing process. They also flag any discrepancies before defective products are produced, saving time and money as well as reputation. LPAs are a verification that appropriate controls are in place and a company’s standard process is being followed in accordance with documented requirements.
LPAs are widely used in automotive manufacturing, and they are now finding their way into other sectors at an increasing rate too. This is especially true of the aerospace industry. Most frequently, quality leaders from the automotive industry migrate to other sectors and implement LPAs as a best practice at their new organisations, knowing they are a vital tool for increasing productivity and ensuring quality is maintained.
Taking inspiration
The electronics industry can learn a lot from the automotive sector, which has long been a global frontrunner in applying and evolving quality improvement tools. In addition to lean manufacturing processes, the automotive sector has been implementing LPA programmes, in its various evolutionary forms, for more than three decades.
Due to the competitiveness of the sector, automotive companies have always needed to evolve their manufacturing process to maximise quality while minimising costs. Demand for vehicles shows no signs of abating either, at a time when modern safety standards and requirements have never been more stringent. Corners can’t be cut.
Through the adoption of LPAs, the automotive sector has enjoyed several benefits, including:
- Reduction of waste
- Improved cash flow
- Improved product quality and customer satisfaction
- Increased ‘right the first time’ results
- Reduced quality incidents (scrap, rework) and escapes
- Reduced the overall cost of poor quality
LPAs have also allowed the automotive sector to evolve with the times. The electronics industry, for which the stakes are so high, needs to follow the automotive sector’s lead and benefit from the impact LPAs can make. The first steps electronics manufacturers should take to ensure LPA success are:
- Form the LPA team
- Conduct a Failure Modes and Effects Analysis (FMEA) to determine where LPAs are needed
- Identify high-risk trends
- Perform a feasibility assessment
- Readjust and refine the LPA programme to suit requirements
- Begin the development process, using the instructions laid out in the LPA programme
- Test, test and test again until the manufacturing process is perfectly refined
Accelerating success
With the pressure and stakes so high for electronic companies to produce and roll out vital products that are in demand internationally, it is time for manufacturing processes to improve. By following the example of the automotive industry, the electronic industry can adopt a robust LPA programme, and ensure that it can continue serving the billions of people across the world who are demanding consumer products almost every day.
www.ease.io
Eric Stoop, CEO of EASE, Inc.