electronics-journal.com
02
'21
Written on Modified on
Connectors for Automotive
Designing a new car is a complex and demanding task. A senior executive at the car manufacturer Ford once said “Cars are far more complicated to engineer than airplanes or Space Shuttles…” By Mark Patrick, Mouser Electronics.
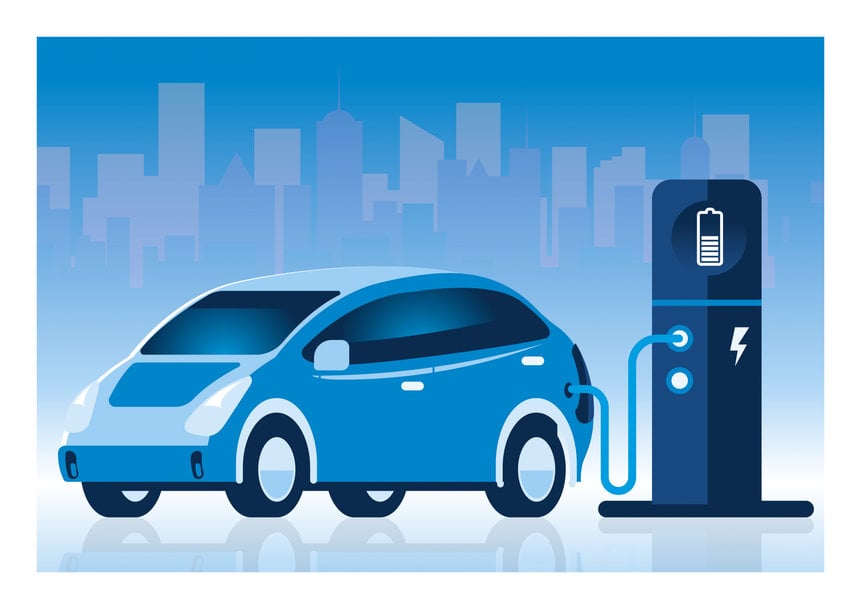
This may sound like a bold statement. With aircraft that cost millions, or spacecraft costing billions, a car may not appear to compete in terms of complexity. However, looking at the question in some detail may reveal the truth behind these words, and how they affect the design of connectors for the automotive world.
The cost of developing a new vehicle is staggering. A quick web search will provide a number of estimates that start at about a billion dollars and rise from there. With such a huge investment required by the manufacturers, it should be little wonder that new cars are designed to be sold to the widest possible global market.
It is this challenge that defines the automotive market, as a new car needs to be able to function in whatever conditions it finds itself. While the automotive environment may not be the most extreme to be experienced by man-made machinery, it is certainly the most diverse.
From the frozen wastes of the arctic to the heat of the desert, vehicles can be subjected to a range of temperatures. In some climates, the variation of temperatures between day and night can exceed 40C, and so any vehicle in this environment must be able to withstand constant temperature cycling on a daily basis for years on end.
To complicate these calculations even further, the car also generates its own heat. The internal combustion engine relies on burning fuel, and parts of the engine and exhaust system experience high temperatures, even if the conditions outside are sub-zero. Designers must consider these extremes carefully, as they will have a major impact on the type of materials selected for major components.
Mechanical reliability is an important consideration. The car contains many moving parts, and these combine with the shock and vibration caused by uneven surfaces. At the same time, components need to be able to resist damage caused by water and other contaminants found on the road.
For decades, connector manufacturers have developed products that offer features with the performance needed for use in the automotive arena. Connectors like the Deutsch DT range from TE Connectivity, the MX150 from Molex or the MX80 from JAE are all designed to cope with the range of conditions that vehicles must face, from extremes of temperature to vibration and shock.
Reliability and Complexity
The environment in which the car operates has a major impact on its reliability. However, customers demand a level of performance that is unheard of in the aerospace world. The reliability of aircraft is sometimes measured by the number of hours of maintenance required for each hour of flying time and, even when maintained correctly, every pilot will still perform visual checks before every flight.
This does not happen in the automotive world. Cars are often only serviced after pre-determined intervals and, despite the advice contained within the user manual, very few drivers perform any kind of check before using their car day-to-day. Drivers simply jump in and expect their car to start on the first attempt, with little consideration of the engineering that goes in to providing this kind of reliability.
One area of the automotive industry that does have parallels with aviation is in the area of complexity. A few decades ago, cars were purely mechanical machines, sophisticated in terms of their moving parts, but simple in their electronics.
This is no longer true. The expectation amongst customers is that manufactures continue to innovate and offer new features with every model they release. Modern family cars now boast electronics that has much in common with 4th generation combat aircraft, from multi-function digital controls and head-up displays to global navigation systems and fly-by-wire operation. As a result, the electronics within a car now represent anything between a third and a half of its overall value.
This change is still underway. The recent advances in V2X (vehicle-to-X) technology will see vehicles become part of a network, communicating constantly with their surroundings. As a result, cars are becoming their own data centres. This has forced manufacturers to adopt technologies that are not ideally suited to the automotive environment.
For many years, connectors have been tested and certified for use in automotive applications according to the SAE/USCAR-2 specification. Connectors are usually installed in pairs, with a female connector terminated to a male or header. When these connectors are tested using the conditions found in cars, the vibration can cause very brief open circuits. The current SAE/USCAR-2 specification seeks to ensure that these discontinuities are limited to no longer than 1 microsecond.
However, cars are becoming hubs of communication that are transmitting, receiving and processing data at Gigabits-per-second speeds. A break in a circuit of a microsecond can cause the loss of thousands of bits of data. This will become a very real problem as the trend towards autonomous or driverless vehicles continues. The safety of passengers, pedestrians and other road users will depend on the faultless performance of systems designed to detect and prevent accidents.
Connectors perform a vital role in the signal path of these new high-speed systems and so the correct choice of connector will be vital for this new generation of highly digitised vehicle. However, the challenging automotive environment will mean that it is not sufficient simply to choose the current breed of high-speed connector, as it will not be able to provide the reliability demanded by the modern automotive industry.
Manufacturers are seeking to solve this problem in a number of ways. The HSBridge+ range from Amphenol has been created to provide high reliability, 5Gbps connectivity for the automotive environment. It has been designed from the outset as a solution for vehicle-based applications.
Other manufacturers are following a different path to automotive reliability. Seeking to capitalise on the latest developments in high-speed connectivity, these manufacturers are testing existing high-speed connectors to standards that are relevant to vehicle-based applications. The tests include intense vibration, humidity and temperature cycling to provide customers with confidence in their suitability for the latest vehicle-based systems.
One manufacturer taking this approach is Samtec, which has developed its own in-house program called Severe Environment Testing (SET). Any product that passes these tests is certified by Samtec to provide customer confidence in its ability to function under harsh conditions. The SEARAY™ connector delivers high speed performance up to 56 Gbps PAM4, making it ideal for the next generation automotive applications.
The automotive environment remains one of the most challenging for designers. Components need to withstand harsh conditions while providing almost unequalled levels of reliability. At the same time, customers are expecting ever-increasing levels of functionality. Choosing connectors for these applications requires a deep understanding of how the conditions will affect their performance. Make sure your design is ready fo the challenges it will face.
LAYOUT NOTE: The following should be inserted as a sidebar
There is an interesting benefit of these products that is not always appreciated. The years of effort that go into developing connectors for vehicle-based applications have created excellent connectivity solutions for designs outside the automotive industry.
Automotive connectors tend to be lightweight, waterproof and robust, and offer significant advantages. Manufactured in huge quantities for the car manufacturers, they are cost effective, easily available and are familiar to cable assembly manufacturers worldwide. These features make them highly interesting to the industrial designer.
www.mouser.com