TDK announces 3D HAL® technology-based position sensor with redundancy for safety-critical applications
TDK Corporation (TSE:6762) announces the portfolio expansion of its Micronas direct-angle Hall-effect sensor family with the HAR 3927**. This product uses proprietary 3D HAL® pixel-cell technology and addresses the need for ISO 26262-compliant development. The new sensor comes with both a ratiometric analog output as well as a digital SENT interface according to SAE J2716 rev. 4.
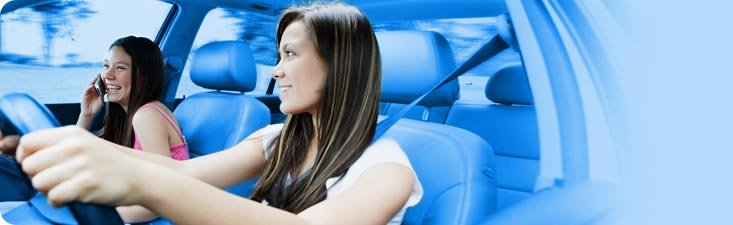
- New dual-die Hall-effect sensor HAR 3927** offers ratiometric analog output and digital SENT protocol according to SAE J2716 rev. 4
- Superior angular measurement and redundancy functions for safety-critical automotive and industrial applications* in a small SOIC8 SMD package
Samples are already available. The start of production is planned for the first quarter of 2022.
The HAR 3927 offers a fully redundant sensor solution for safety-critical automotive applications, such as linear-movement measurements in dual-clutch transmissions, engine stroke sensors, rotary position measurements in gear selectors and accelerator pedals, and electronic throttle control*.
Each HAR 3927 sensor contains two stacked dies that operate independently. The dies have minimal displacement and are penetrated by the same field lines. The HAR 3927, compared to other solutions with two dies side by side, operates with significantly smaller magnets. Its magnetic field amplitude range is 20 mT to 130 mT, and down to 5 mT with reduced accuracy.
The HAR 3927 is available in a miniature eight-pin SOIC8 package. The redundant single-package solution reduces system costs while increasing the reliability of the system due to smaller PCBs and less solder joints.
The sensor offers two different output formats and a linearization block for an output signal of up to 33 setpoints (17 variable or 33 fixed setpoints). Due to the proprietary 3D HAL pixel-cell technology, customers can measure magnetic-field components, enabling linear and rotary position measurements up to 360°, as well as on-and-off-axis measurements. Primary characteristics like gain and offset, reference position, etc. can be adjusted to the magnetic circuitry by programming the non-volatile memory.
Various configuration options of HAR 3927 increase customers’ flexibility during development and enable one sensor to be used in multiple applications, which reduces costs and effort for re-qualification.
Glossary
3D HAL® pixel cell: Enables the direct measurement of magnetic fields in three directions X, Y, Z.
Main applications*
- Detection of angle of rotation in automotive applications, such as accelerator pedal, electronic throttle control, rotary shifters (with push-function), as well as rear-axis steering systems
- Detection of linear position in applications like clutch or brake pedal, transmission system, cylinder and valve position sensing
Main features and benefits***
- Very low angular error of ±1.0° @ 30 mT amplitude
- End-of-shaft and off-axis 360° angular measurement
- Direct measurement of magnetic-field amplitude (BX, BY, BZ)
- Customer-selectable analog or SENT output
- Full redundancy due to Dual-Die approach
- SEooC according to ISO 26262 to support functional-safety applications
- Suitable for automotive applications, due to a wide ambient temperature range from -40 °C to 160 °C
Key data
* Any mention of target applications for our products are made without a claim for fit for purpose, as this has to be checked at system level.
** HAL/HAR 39xy uses licenses of Fraunhofer Institute for Integrated Circuits (IlS)
*** All operating parameters must be validated for each customer application by customers’ technical experts.
www.tdk.com