electronics-journal.com
10
'24
Written on Modified on
TDK presents enhanced embedded motor controllers with increased memory, power, and reliability
Capable of 4 x 1 A peak current for driving brushless DC (BLDC), brushed DC (BDC), and stepper motors. Featuring 4 KB SRAM, 2 KB EEPROM in 32 KB, and 64 KB flash memory variants.
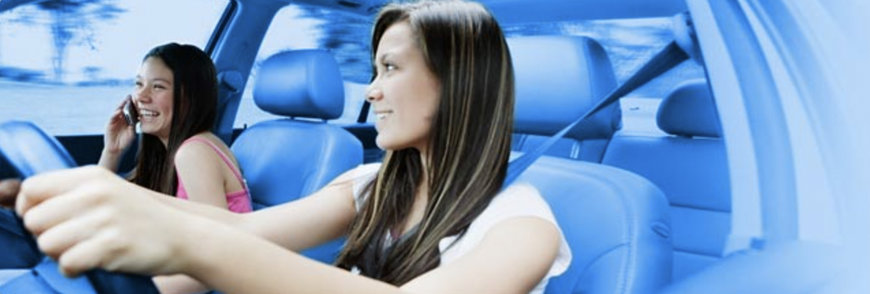
TDK Corporation further extends its Micronas embedded motor controller family, HVC 5x, of fully integrated motor controllers with HVC 5222D and HVC 5422D to drive small brushed (BDC), brushless (BLDC), or stepper motors. They offer significant enhancements compared to the popular HVC 5221D, doubling drive current, SRAM, and 4x EEPROM while maintaining pin compatibility. Samples are now available for customer evaluation. Start of production is planned for the first quarter of 2025.
The latest motor controller models, HVC 5222D and HVC 5422D, feature expanded flash memory capacities of 32 KB and 64 KB respectively, support currents up to 1 A for BLDC and stepper motors, and up to 2 A for DC motors, along with advanced motor-specific functions such as current programming for micro-stepping and integrated phase voltage comparators, virtual star-point, and current sense amplifier for sensor-based and sensor-less motor control, meeting ISO26262 standards for ASIL applications.

The HVC family has expanded to include nine fully integrated motor controllers featuring three to six motor outputs, capable of delivering peak currents ranging from 500 mA to 2 A. Each device is powered by a 32-bit Arm® Cortex®-M3 CPU core, offering options of 32 KB or 64 KB Flash Memory. Equipped with a 12-bit, 1-µs ADC for diverse measurements, these devices allow seamless integration of Hall and TMR sensors from TDK. Additionally, the HVC family devices come with a LIN transceiver and UART for communication, supporting auto-addressing via the Bus Shunt Method (BSM), enhancing their adaptability across various applications. PWM control via the LIN pin is also supported. Certified to automotive standards AEC-Q100 for temperature Grade 1, all HVC devices ensure reliability, catering to automotive and industrial applications with power requirements of up to 30 W.
Glossary
- AEC-Q100: Qualification standard for automotive applications
- ADC: Analog to Digital Converter
- BDC: Brushed DC motor
- BLDC: Brushless DC motor
- BSM: Bus Shunt Method for LIN auto addressing
- CPU: Central Processing Unit
- Grade 1: Ambient temperature 125 ºC, junction temperature 150 ºC
- HVC: High Voltage Microcontrollers
- LIN: Local Interconnect Network for automotive applications
- QFN: Quad Flat No Lead package
- UART: Universal Asynchronous Receiver / Transmitter