electronics-journal.com
22
'21
Written on Modified on
Delta Cotton Swabs’ Automatic Inspection and Packaging Solution Enhances Product Quality
Smart Manufacturing Integrates Machine Vision and Industrial Robots
Many people cannot imagine a day without using cotton swabs. Behind such a small product, there is extensive know-how from production to packaging. Since the unit price is relatively low, the investment in time and resources is highly sensitive. To optimize results, the cotton swabs must be quickly placed into a package in order. This is a challenge for traditional manufacturers that mainly rely on manual labor.
Yet another challenge, is that there is an ever increasing shortage of manpower in the manufacturing industry. To enhance productivity and maintain a consistent product quality, many manufacturers adopt automated equipment and processes. On top of that, smart manufacturing is becoming an unstoppable trend. To prepare for this new era, building highly automated production lines has become a necessary move for the future.
Delta recently built a cotton swabs’ automatic inspection and packaging solution for a packaging partner working with a cotton swab manufacturer. The solution integrates a vibration bowl, conveyor belts, industrial robot, and machine vision for an all-in-one automatic machine. It improves overall performance with higher productivity and longer runtime. In addition, the adoption of machine vision avoids the inconsistencies of manual inspection and ensures product quality.
The solution includes the High-Performance Slim PLC DVP-SV2 Series that delivers cotton swabs from a vibration bowl and transfers them to the inspection spot under the Machine Vision System DMV2000 Series. The SCARA Robot DRS40L Series then tracks the conveyor and picks-and-places the qualified ones into the case in a set order. While the robot sends a signal to the PLC for counting, the pick-and-place movement stops when it reaches the set number. The PLC controls the positioning cylinder to switch to a new case and enable a smooth process for packaging and inspection.
Delta cotton swabs automatic inspection and packaging solution provides the following benefits and advantages for the manufacturer and users:
• Automated production line enhances productivity
The automated production line integrates the 10.1-inch Widescreen Ethernet HMI DOP-110 Series, High-Performance Slim PLC DVP-SV2 Series, and SCARA Robot DRS40L Series. It extends runtime and enhances productivity.
• Machine vision maintains consistent product quality
Unlike manual inspection, the Machine Vision System DMV2000 Series avoids distraction and can quickly and precisely detect defects and maintain the consistency of product quality.
• Quick pick-and-place ensures the package counts
Delta’s SCARA Robot DRS40L Series quickly tracks the conveyor and sends signals to the High-performance Slim PLC DVP-SV2 Series to count whether the quantity of cotton swabs has reached the set number, and ensures the accuracy of each case.
Delta’s cotton swab automatic inspection and packaging solution integrates PLC, machine vision, and industrial robot in an all-in-one machine. It decreases the need for space and is capable of quick and precise packaging. Besides, it helps users overcome labor shortage challenges. The solution is highly automated and flexible for industrial 4.0, which may help users embrace the potential and opportunities of smart manufacturing.
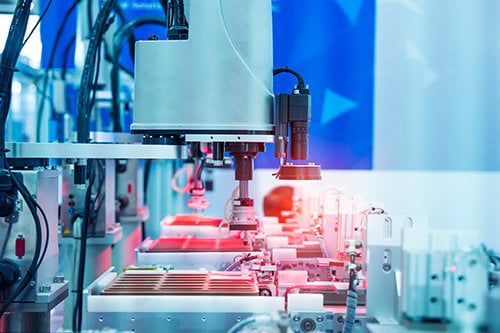
Delta recently built a cotton swabs automatic inspection and packaging solution for a customer. The solution adopts machine vision to avoid manual inspection inconsistencies and maintain product quality.
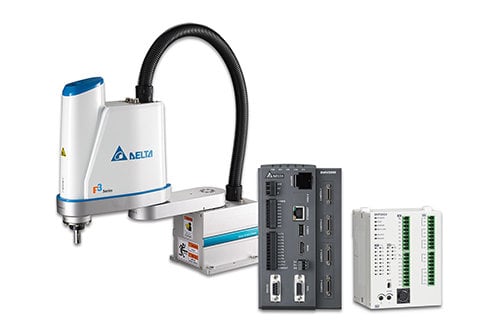
Delta integrated the High-Performance Slim PLC DVP-SV2 Series (Right), Machine Vision System DMV2000 Series (Middle) and SCARA Robot DRS40L Series (Left) to ensure a smooth packaging and inspection process.