Battery Show 2021: latest innovations and advanced solutions for the clean mobility
Arkema will be present at the Battery Show held on 30th November to 2nd December 2021 at Stuttgart and will exhibit its unique portfolio of innovative, durable and sustainable materials and its process expertise from cell to module and battery pack assembly up to battery system integration into the vehicle.
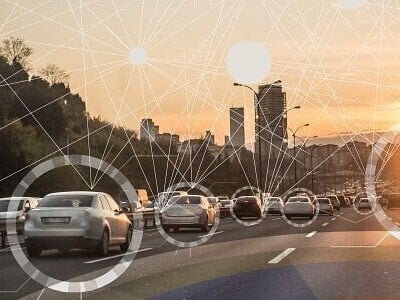
To address the fast-growing demand for materials in batteries, Arkema accelerates its investments and mobilizes its research capacities.
Thanks to its recognized expertise and broad technology portfolio, Arkema is ideally positioned at the heart of the battery ecosystem to support its customers and partners in the clean mobility revolution. Arkema is thus one of the world's leading suppliers of high value-added solutions:
At the heart of each cell:
- Although characterized as an inactive material, the Kynar® PVDF HSV cathode binder is an extremely active material in the electrode at various stages. As a key enabler in electrode manufacturing, its design allows for outstanding performance throughout the cells service life.
- Kynarflex® LBG series is the “to go” solution for an efficient coating when it comes to separators and achieving the goal of outstanding adhesion with the electrodes for better performance. This versatile technology can be used either in Solvent or Water based coatings.
- Foranext® ultra-pure electrolyte salts, far more stable at high voltage than current solutions, will help to reduce the battery’s charging time and increase its autonomy.
- Graphistrength® carbon nanotubes, added to the cathode in small quantities, help the flow of electrons to the anode and reduce battery charge time.
Inside the modules:
- Rilsan® polyamide 11, 100% bio-based from sustainable castor plant, provides electrical insulation in thin layer of intercell cooling plates.
- Piezotech® piezoelectric polymers are used as “actuators” for sensors monitoring the level of battery charge.
- Bostik® specialty adhesives, well adapted for the cell assembly of all different cell types, are used to attach cells to each other and to the module or pack casing.
For thermal management:
- Rilsan® polyamide 11, is widely used for battery cooling lines, which require good thermal control to insure optimal performance and durability of the battery. Tubes made of Rilsan® Polyamide 11 allow the transfer of cooling liquid to and from the radiator and battery pack. Rilsan® Polyamide 11 combines very good mechanical strength, durability and easy assembly to the battery.
- Bostik® thermal conductive gapfillers and adhesives ensures efficiency and durability of lithium ion batteries by transferring the heat in the battery system to maintain optimized temperature levels guaranteeing reliable and long-term battery operations.
For battery management system:
- Rilsan® polyamide 11, used as a protective coating for busbars, can be offered as powder for metal coating application or as pellets for cross-head extrusion and injection application. It offers electrical insulation, thermal resistance and bendability. Busbars, which link modules to each other, are used instead of flexible cables to make the battery more compact.
- Bostik® encapsulation adhesives for electronic components, based on hot melt polyamide and UV cyanaocrylate technologies, provide protection from any damage for the most sensitive electronics, for both low-pressure molding processes and conformal coating applications.
For battery assembly:
- Bostik® battery pack sealing and gasketing adhesives ensure the save and reliable enclosure of the pack, helping to meet its overall performance needs for temperature resistance and sealing, while providing the option to be removed to enable repair and recycling.
- Bostik® structural adhesives are used to assemble the battery pack housing and other types of components for and in the battery pack, such as the cooling plate.
For the protection pack:
- Elium® thermoplastic resin, used as a high-performance composite matrix, is the preferred choice of a growing number of manufacturers for the battery pack as an alternative to steel, in comparison to which it presents a considerable weight advantage.
- Kepstan® PEKK, thanks to its light weight and outstanding resistance, offers a high-end battery pack protection solution.
- Bostik® battery pack lamination adhesives, used to laminate an aluminum foil onto the composite battery pack to ensure excellent EMI shielding protection, complete the solution offer for battery pack light weight designs.
New capacity for sustainable solutions
Arkema is one of the world's leading suppliers of PVDF for cathode binders and separator coatings as well as bio-based polyamide 11 for battery busbars coatings and battery cooling lines.
To support the exponential growth in demand for lithium-ion battery cell materials, Arkema announced recently a 50% expansion of its Kynar® fluoropolymer production capacity at its Pierre-Bénite site in France. New innovations and product ranges will also be offered, such as Kynar® CTO, the new Kynar® PVDF range made from renewable sources. This new extension should come on stream in the first quarter of 2023. Earlier this year, Arkema also announced an investment to increase fluoropolymer production capacities in Changshu, China by 35% in 2022. This increase in capacity is scheduled to come on stream before the end of 2022.
Further, Arkema is on track to begin production of Amino 11 and its flagship Rilsan® Polyamide 11 at its new plant on Jurong island, Singapore in the first half of 2022; This plant, for which production will be 100% derived from renewable castor beans, represents a 50% increase in Arkema’s global polyamide 11 capacity. More recently, Arkema announced the construction of a polyamide 11 powders plant on its Changshu platform in China, scheduled to come on stream in the first quarter of 2023. This investment will further support the growing demand for advanced bio-circular materials in Asia.
As part of Arkema’s ongoing development of sustainable solutions Arkema also announced recently additional capacity of fluorinated specialty solution 1233zd for new fields of application in battery thermal management of electrical vehicles, expected to start in late 2023.
Shared knowledge and collaborative research
On 19th November, Arkema inaugurated a Center of Excellence to batteries at its Pierre-Bénite Research Center. This Center of Excellence will help accelerate the development of advanced materials and processes for e-mobility, but also for stationary uses, renewable energy storage and electronics, improvements in battery performance including greater energy density and shorter charging time, greater autonomy and lighter weight of vehicles. The teams will conduct research with academics, as well as with partners in the battery ecosystem.
www.arkema.com